-
-
Delivering
INTELLIGENT
ENGINEERING
Across Industries -
Cyient Wins
PREMIER AWARD FOR
EXCELLENCE FROM RTX
for Third Straight Year
The next decade of engineering is being shaped by megatrends such as Smart Operations, Intelligent Meta Mobility, Digital Healthcare, Sustainability, and Space Systems, all driving significant investments across industries. With ER&D spend projected to grow at a 10% CAGR over the next three years—and advanced technologies leading the way with a 19% CAGR—enterprises have a unique opportunity to stay ahead of the curve. Those who align with these trends aren’t just future-proofing their operations; they’re reimagining possibilities for growth and innovation.
At Cyient, we design, build, and maintain products, plants, and networks, making them intelligent through the power of advanced technologies. By leveraging AI, data analytics, cloud computing, and 5G, we solve critical problems with purpose and precision. We call this unique approach Intelligent Engineering—where imagination meets transformation to create meaningful impact.
Designing Tomorrow with Engineering Excellence
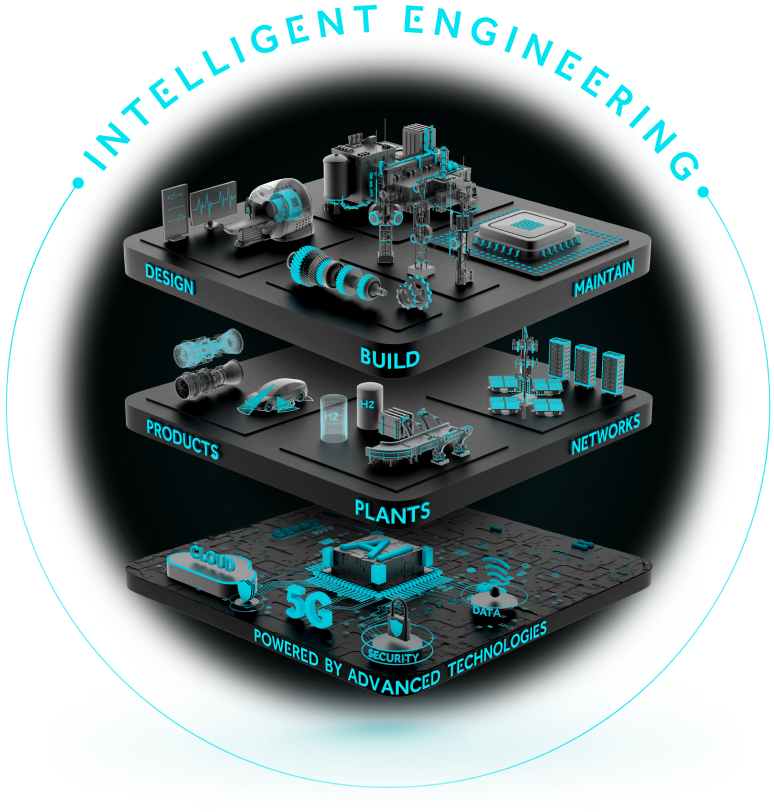
-
POWERED BY ADVANCED TECHNOLOGIES
- Cloud Platforms for Engineering Workflows
- 5G for Private Wireless Connectivity
- Enabling Security for Next-Gen Products
- IoT-Enabled Connected Plant and Manufacturing
- EnGeneer CoE for AI in PDLC
-
PRODUCTS
- Digital Twin & Digital Thread
- Autonomous Systems
- Connected Products
- Electrification
- Silicon
- Software
- Embedded
- Mechanical & Electrical
- Industry 4.0
- Aftermarket
-
PLANTS
- Industry 4.0
- Autonomous Plant
- Carbon Capture & Storage
- Plant Design
- Supply Chain Management
- Operations & Maintenance
- Asset Management
-
NETWORKS
- AI-Driven Network Management
- Zero Touch Automation
- Digital Twin Modeling
- Energy Scoring
- Copper Reclamation
- Network Design & Rollout
- Data Lifecycle Management
- Network Operations & Maintenance
- Network Testing & Security
-
POWERED BY ADVANCED TECHNOLOGIES
- Cloud Platforms for Engineering Workflows
- 5G for Private Wireless Connectivity
- Enabling Security for Next-Gen Products
- IoT-Enabled Connected Plant and Manufacturing
- EnGeneer CoE for AI in PDLC
-
PRODUCTS
- Digital Twin & Digital Thread
- Autonomous Systems
- Connected Products
- Electrification
- Silicon
- Software
- Embedded
- Mechanical & Electrical
- Industry 4.0
- Aftermarket
-
PLANTS
- Industry 4.0
- Autonomous Plant
- Carbon Capture & Storage
- Plant Design
- Supply Chain Management
- Operations & Maintenance
- Asset Management
-
NETWORKS
- AI-Driven Network Management
- Zero Touch Automation
- Digital Twin Modeling
- Energy Scoring
- Copper Reclamation
- Network Design & Rollout
- Data Lifecycle Management
- Network Operations & Maintenance
- Network Testing & Security
-
POWERED BY ADVANCED TECHNOLOGIES
- Cloud Platforms for Engineering Workflows
- 5G for Private Wireless Connectivity
- Enabling Security for Next-Gen Products
- IoT-Enabled Connected Plant and Manufacturing
- EnGeneer CoE for AI in PDLC
Delivering Engineering Excellence Across
33 Years of Engineering Excellence
Across Industries
Solving Problems that Matter
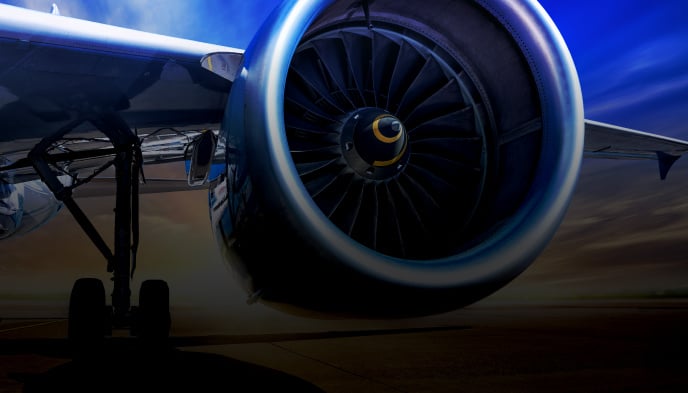
Cut 3.1M Tons of CO2 with the World’s Greenest Engine
Designed the world’s most fuel-efficient aircraft engine—reducing CO2 emissions by 3.1M metric tons, improving efficiency by 5% in just 3 years, and making air travel more sustainable for future generations.
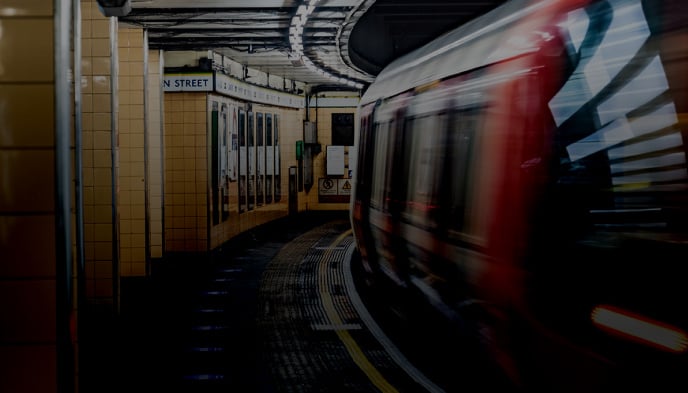
Safer, Faster Commutes for 2M Londoners
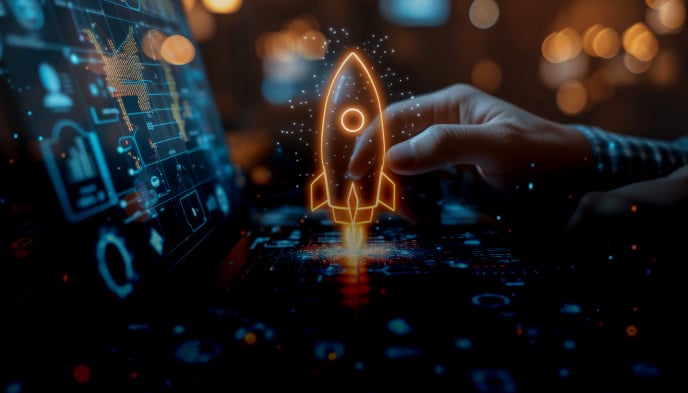
Elevated Customer Experience with Digital Innovation
Built SPARK, a subscription-based digital collaboration platform driving aftermarket transformation. Using a risk-sharing model, it enhances customer experiences, streamlines operations, and supports long-term innovation with 300+ scalable digital solutions.
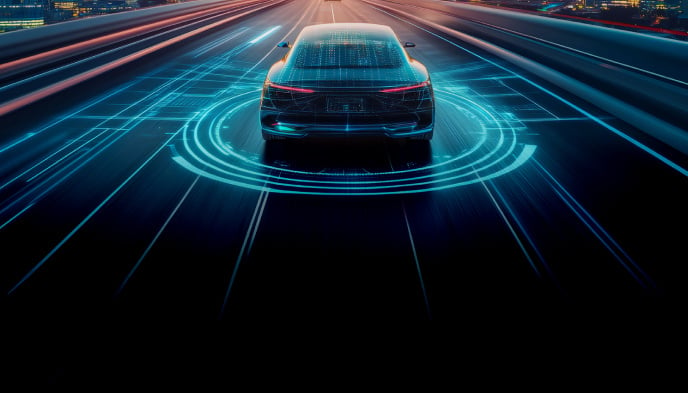
AI-Driven Perception for Safer Autonomous Vehicles
Enhanced autonomous vehicle safety with an AI-powered Perception System. Using sensor fusion and AI, it enables precise object detection for safer navigation in complex environments, improving both road and off-highway operations.
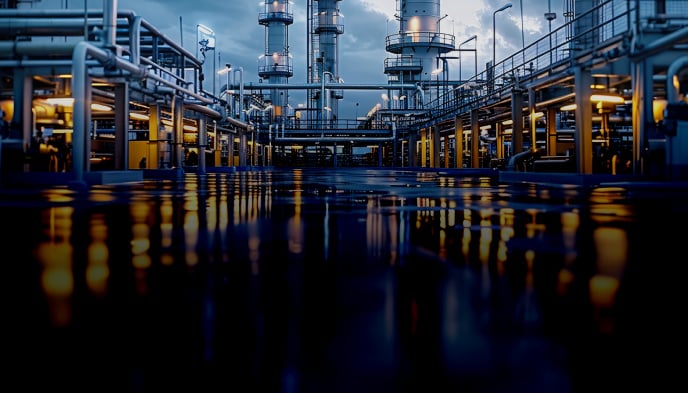
250MW of Clean Energy for a Sustainable Future
Designed and documented a 250MW tri-fuel power plant in Jordan, optimizing efficiency and sustainability. Engineered a fire-safe fuel storage system and water-efficient cooling to meet strict regulations.
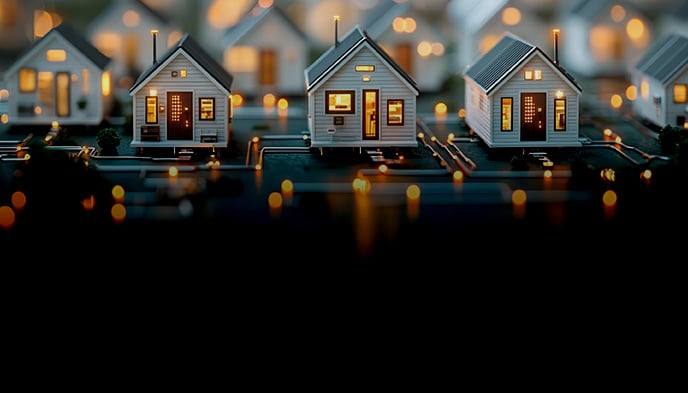
Connected 60M Homes, One Community at a Time
Delivered high-speed connectivity to 60M homes worldwide, empowering families, businesses, and communities while supporting NetZero goals.
50% of Our Customers
Trust Us as a Strategic Partner
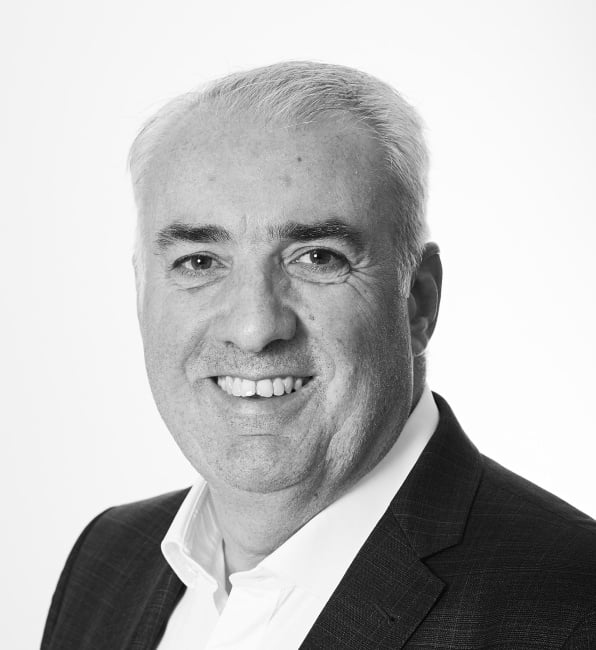
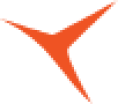
Cyient’s vast experience in A&D makes them an ideal design partner for D328eco Program
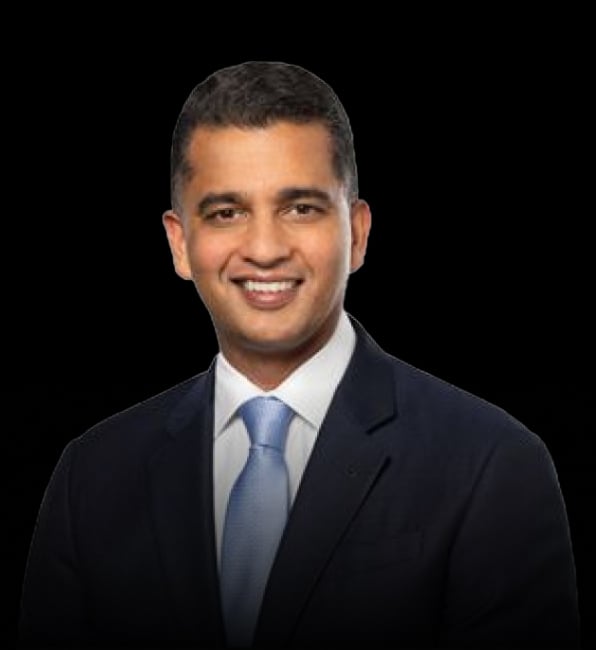
Watch Now
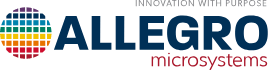
Our collaboration with Cyient has helped us strategically position Allegro in this dynamic landscape
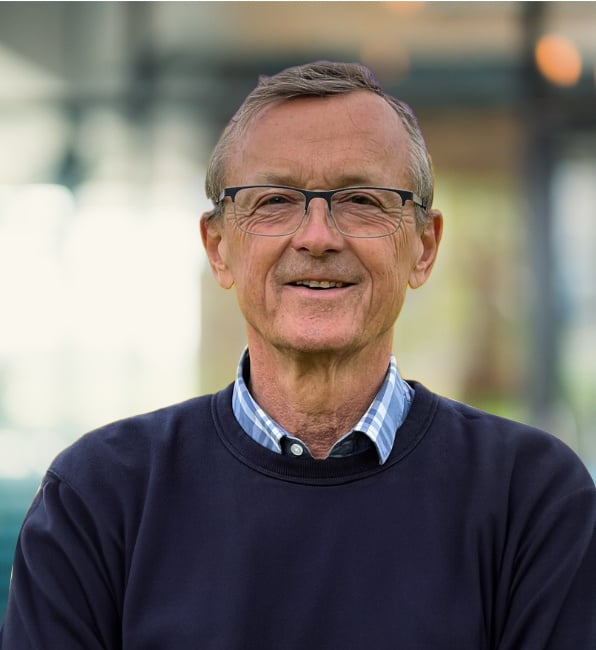
In my 20 years as an R&D leader in several Philips businesses, Cyient has been a reliable partner to me, providing invaluable support in addressing challenging issues, fulfilling sudden resource requirements, and delivering specialized long-term services. The seamless collaboration with Cyient, characterized by a lack of friction, has been particularly noteworthy. Their team consistently acts and feels like an extension of our internal staff. Additionally, their diversity ensures the availability of tailored solutions for every challenge encountered.
.png)
The Hafslund Oslo Celsio CCS project in Norway can contribute invaluable knowledge and experience to the industry as a whole, including the 450 waste-to-energy plants across Europe. The carbon capture project is essential for Oslo to have the opportunity to achieve its climate goals in 2030. Realizing this project will give significant learning to other Norwegian and European cities that have targets for climate-positive waste handling. We are highly appreciative of Cyient’s partnering attitude, expertise, and quality of deliverables throughout the project's different demanding phases.
Innovation is in Our DNA

The Cyient Forum for Innovation Quotient – is a 360 degree innovation forum where
imagination meets action to solve problems that matter. Combining core engineering
expertise with advanced technologies, we develop IP-driven accelerators, platforms, and
solutions to prepare industries for the future. Our 30+ platforms and solutions include
flagship offerings like Platform X for cloud integration, IntelliCyient for Industry 4.0
transformation, and Industry AI Advisor, a Gen AI platform for personalized AI
assistance. With a diverse ecosystem of partners, startups, academia, and labs,
CyientifIQ drives collaborative innovation to deliver intelligent engineering solutions
across industries, from manufacturing to aerospace and beyond.
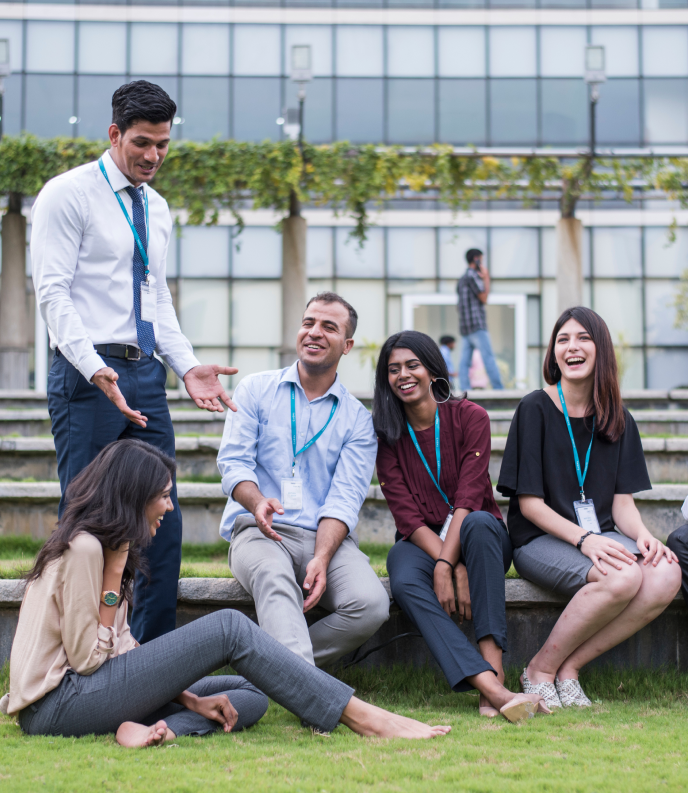
People
at the Core
With over 16,000 proud Cyientists from 22 nationalities, we celebrate our differences and leverage them to create a collaborative and inclusive atmosphere. This vibrant diversity not only fuels our innovative spirit but also fosters a workplace environment where everyone feels valued and empowered to contribute, making Cyient a truly great place to work.
One Earth, One Chance
Committed to a Sustainable Future
0 th
Percentile Ranking in
ESG Reporting
0 %
Renewable Energy-led
Operations
Go Green
Single-use,
Plastic-free Offices
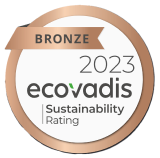